Sodium bicarbonate (baking soda) raw material is uniformly fed into the chamber through a quantitative feeder at the lower part of the silo, which grinds raw material into a particle size of D90:20μm, allowing to adjust particle size according to specific requirements. The high-pressure fan then conveys the powders into the pipeline and sprays it directly into the flue gas, quickly reacting with acid gases and decomposing them into sodium carbonate (Na2CO3), H2O, and CO2 at high temperatures. Newly generated sodium carbonate has an incredibly high reaction activity that efficiently reacts with acidic substances in the flue gas.
NaHCO3 + HCl → NaCl + H2O + CO2
2NaHCO3 + SO2 + ½ O2 → Na2SO4 + H2O + 2CO2
NaHCO3 + HF → NaF + H2O + CO2
- Dry process desulfurization Desulfurization by dry process can remove more than 95% of SO2 and 99% of HCl in the tail gas.
- Easy to disassemble and wash Compact structure, easy to disassemble and wash. Cleaning In Place (CIP) optional, reducing downtime by removing stucked material.
- Quick maintenance Quick maintenance with power-assisted flip device and manhole for fan
- Low investment & operation cost Imple and reliable process, ensuring low investment, low operation cost and short construction period
- Low failure rate and stable operation Stable operation and low failure rate, suitable for continuous running up to 8000 hours per year
- Large air intake design Large air intake design reduces grinding temperature; cold air device available if needed
- Clean and environmentally friendly Closed loop system produces less dust, low noise, supporting a clean and environment-friendly production process.
- Non-irritating and non-toxic Non-irritating/non-toxic additive (sodium bicarbonate) & residue
- Integrated design of grinding and classifying Grinding & classifier integrated design allows adjustable particle sizes by adjusting the rotating speed.
- Intelligent control system Intelligent control system with one-key operation & in-place monitoring of sulfur dioxide concentration, system air volume, feeding volume, grinding temperature, etc.
- Narrow particle size distribution The particle size adjustable between D90: 10-40 μm, with good particle shape and narrow distribution
- Automatically adjusting the injection of the desulfurizing agent Automatically adjusts injection amount of desulfurizing agent according to flue gas concentration fluctuation
TSM parameter | 300 | 400 | 500 | 630 | 800 | 1000 | 1250 |
Grinding disc diameter (mm) | 280 | 410 | 510 | 630 | 800 | 1000 | 1200 |
Grinding disc power (kW) | 7.5 | 18.5 | 22 | 37 | 55 | 75 | 110 |
Classifier power (kW) | 3 | 5.5 | 7.5 | 15 | 18 | 22 | 30 |
Production capacity for D90:20μm (kg/h) | 10-80 | 50-150 | 100-200 | 200-400 | 300-600 | 500-1000 | 1200-2000 |
Note: The particle size, specific gravity, hardness, and moisture of raw materials are all closely associated to the production capacity. These parameters should only be used as a reference; for more detailed information please consult our engineers.
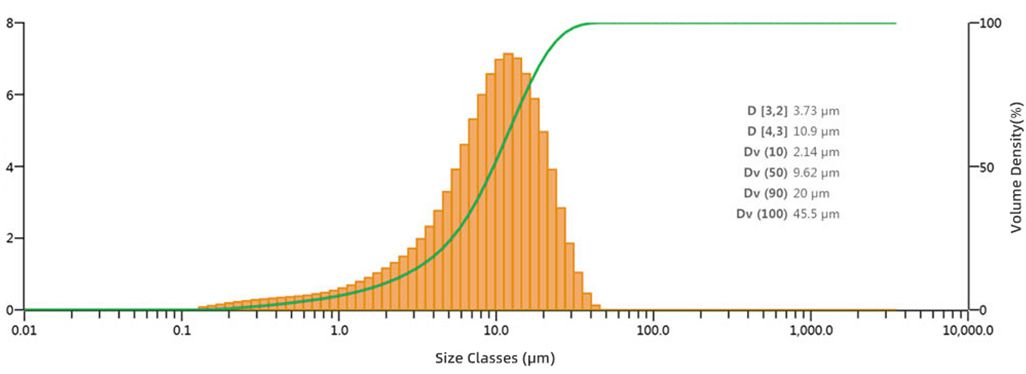
Classic model TSM500
Used by a number of environmental protection companies in the desulfurization processGiant mill TSM1250
Exported to Europe for desulfurization projectsBaking soda desulphurization mill
High-precision mechanical mill, special model 710 for baking soda desulfurization