The Ring Roller Mill uses a main shaft that rotates to drive a rotor frame. An auxiliary shaft is arranged on the rotor frame, and grinding discs are attached to this auxiliary shaft. As the main shaft rotates, it causes the grinding discs to not only revolve around its axis but also rotate around their respective auxiliary shafts.
This generates a strong centrifugal force which has an intense rolling action with discstatic disc of the Ring Roller Mill. The ground material is then forced into the chamber between the static disc and grinding disc where they are ground under great pressure, before being thrown by a material throwing disc onto a shunt ring located between the machine body and static disc. Here, it is classified according to size with fine powder entering into collection system while coarse particles fall back into grinding chamber for re-grinding.
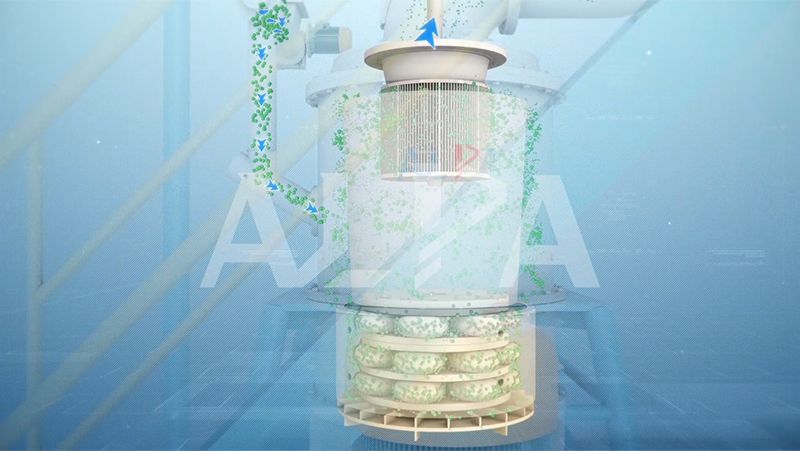
Parameter | RLM89 | RLM189 | RLM219 |
Production capacity for D97:28μm (kg/h) | 4500~5000 | ||
Production capacity for D97:18μm (kg/h) | 2500~2800 | 3500~4200 | 3500~4200 |
Production capacity for D97:10μm (kg/h) | 1500~1800 | 2000~2500 | 2000~2500 |
Production capacity for D97:9μm (kg/h) | 1000~1300 | 1500~2000 | 1600~2100 |
Production capacity for D97:7.8μm (kg/h) | 650~750 | 1000~1500 | 1100~1600 |
Production capacity for D97:5.5μm (kg/h) | 600~650 | 800~1200 | 900~1300 |
Power (kW) | 152 | 237 | 237 |
Note: The particle size, specific gravity, hardness, and moisture of raw materials are all closely associated to the production capacity. These parameters should only be used as a reference; for more detailed information please consult our engineers.